We produce most of the solar energy related products, such as Solar Photovoltaic Panels, Grid Cabinets, Energy Storage Batteries, Photovoltaic energy storage inverter, Small Busbar, Portable Power......
energy storage welding sheet metal process
- Home
- energy storage welding sheet metal process
Achieve Perfect Spot Welding: The Ultimate Guide
In achieving a perfect weld, a range of variables come into play: Electrode Force: Dictates the quality of the weld. Squeeze Time: The lull between applying force and initiating the current. Welding Time: The span during which the current actively flows. Holding Time: Period for the nugget to solidify.
Ultrasonic Metal Welding Evolves to Meet Energy Storage …
Ultrasonic welding can join nonferrous metals like copper & aluminum to each other as well as to mild steels. New systems employ a novel approach called "direct …
Parametric Study of Spot Welding between Li-ion Battery Cells and Sheet Metal …
This work was designed to study the effects of influencing parameters in series/parallel gap spot welding process and determine the optimized parameters setting for spot welding between 18650 Li-ion battery cells and sheet metal connectors.
3 Methods of Welding Sheet Metal: Which Do You Need?
3 Methods of Welding Sheet Metal: There are many different methods for sheet metal welding, but the three we are going to discuss are MIG (metal inert gas), TIG (tungsten inert gas), and laser welding. The method used will depend on many factors. Below are things to consider for each of the three methods.
126 Resistance Spot Welding of AA5052 Sheet Metal of Dissimilar Thickness …
Resistance spot welding of dissimilar thickness of AA5052 aluminum alloy was performed in order to investigate the effect of metal thickness combination on the weldability of this alloy. Increasing in materials thickness increased the nugget diameter, welds time and coarsened the microstructure. As thickness of sheet metal increased, the ...
Comprehensive energy-saving method for sheet metal forming
Sheet metal forming is also an energy-intensive process in manufacturing and consumes a large amount of energy because of its low energy efficiency. In this …
Plug Welding Sheet Metal – Mastering the Art of Joining Metal …
Ensuring Proper Fit and Overlap: Align the metal sheets to achieve the desired joint configuration, ensuring that they overlap to the specified dimensions for plug welding. Utilize clamps or magnets to secure the sheets in position, maintaining the required overlap for the welding process. Marking the Weld Locations: Mark the precise …
Sheet Metal Welding: An Overview of the Process
Welding with gas MIG, or gas metal arc welding, is an excellent method for welding sheet metal. It combines a continuous solid wire electrode with inert shielding gas to form a weld puddle. This welding process uses aluminum, stainless steel, and mild steel. It produces high-quality, consistent welds and is popular for many projects.
What Is Tack Welding? Understanding Its Purpose …
Although a temporary fixture, tack welding is very important to the success of welding generally. Its major functions during the welding process include: Ensuring proper alignment of materials. …
Welding Sheet Metal Guide (Updated for 2024) | Approved Sheet …
In an effort to demystify welding and help our customers choose the optimal welding method for a part, we do our best to clearly outline the benefits and …
Precision Sheet Metal Fabrication Process: An Overview
The precision sheet metal fabrication process involves producing precise sheet metal components for vehicles. The process begins with design, followed by cutting, forming, joining, finishing, quality control, and packing. #1. Design Phase. The design phase begins with creating detailed technical drawings and blueprints using Computer-Aided ...
9 Different Types of Sheet Metal Operations with …
3. U-bending. In this type of a bending operation, in which when the punch is pressed by a force to move into the die, the sheet metal piece gets formed into a U-shape. 4. Offset Bending. It is a type of …
Submerged Arc Welding (SAW): Definition, Purpose, and How It …
14 min read. Submerged arc welding (SAW) is a well-established process that uses a continuous feed of a filler/electrode, melted by an electric arc between the electrode/filler and the work. Submersion refers to the hopper-fed flux powder that covers the weld path. This approach allows greater control and automation of straightforward welds.
Welding
Overhead stick welding Welding is a fabrication process that joins materials, usually metals or thermoplastics, primarily by using high temperature to melt the parts together and allow them to cool, causing …
Stored Energy Welders | AMADA WELD TECH
The Stored Energy welding power supply – commonly called a Capacative Discharge Welder or CD Welder – extracts energy from the power line over a period of time and stores it in welding capacitors. Thus, the effective weld energy is independent of line voltage fluctuations. This stored energy is rapidly discharged through a pulse transformer ...
Spot Welding: In-Depth Guide & Techniques Revealed
For low-carbon steel sheets with a thickness of 1-1.5 mm, the maintenance time is 0.1-0.2 seconds, while for welding low-carbon steel with a thickness of 8-10 mm, the full crystallization of the welding nucleus requires around 1.5-2.5 seconds. Therefore, the maintenance time should not be less than this value.
Sheet Metal Welding Methods. MIG, TIG, MAG, GTAW & GMAW Welding …
Gas welding. Another relatively simple technique for welding of sheet metal is with the help of burning some form of gas – oxygen, fuel or oxyacetylene – to melt parts of sheet metal and join them together while they are melted. This is a fairly common process in the industry, and also one of the older ones on the list.
Sheet Metal Welding: Process, Types and Tips
Sheet metal welding is done by heating two thin sheets of metal to melting point. The melted sheets are then skillfully joined together using a torch to form the desired shape and specifications. 1. Flat Surface. When welding a flat surface, the welder points the torch from the upper side of the joint.
Welding methods for electrical connections in battery systems
The techniques investigated in this project are resistance-, laser and ultrasonic metal welding. APR provided a template containing research topics that were of greater …
Welding Sheet Metal with Flux Core
Table of Contents. Choosing the appropriate flux core for sheet metal. How to weld sheet metal with flux core. Prepare your workpiece. Set up the metal. Adjust the welder to the proper settings. Weld the sheet metals. Remove spatter and slag. To sum up …
Stud Welding Methods | STANLEY® Engineered Fastening
With drawn arc stud welding, the operator uses a weld tool, or gun, to place the stud against the base metal. When triggered, an electric solenoid in the gun lifts the stud to a preset height off the base metal. The drawn arc melts the base of the stud and the base metal, creating a molten pool. The gun then forces the stud down into the molten ...
How to Weld Sheet Metal: Advanced tutorials from novice to expert
The minimum thickness suitable for welding largely depends on the welding technique used. Typically, you can weld sheet metal as thin as 0.5mm (around 0.02 inches) with processes like MIG or TIG welding. However, welding thin sheet metal requires precision and skill to prevent burn-through and warping.
Automation of Spot Welding between Li-ion Battery Cell and Sheet Metal …
International Journal of Novel Research and Development () h331. II. NEED OF THE STUDY. The need to enhance the spot welding process for lithium-ion battery cells and sheet metal connectors has prompted a shift towards automation solutions. By adopting automated systems, manufacturers can overcome the limitations of manual spot ...
What is Resistance Welding? Process, Diagram, Types
Figure 6: Energy Storage Welding. Welding is obtained by discharging the stored energy in the capacitor. As shown in Fig. 6, it consists of a bridge rectifier, capacitor, switching arrangement. The pieces to be welded are kept at a certain distance apart (1.5 mm).
Sheet Metal Processes – EngineeringTechnology
Embossing, is a process used to create raised or sunken designs or patterns on the surface of a metal sheet. It involves using specialized tooling and presses to deform the metal, resulting in a three-dimensional pattern. Embossing is often employed for decorative or functional purposes, such as adding texture, branding, or strengthening the ...
Sheet Metal Forming: How It Works, Processes, and Uses
Sheet metal forming makes use of a number of processes to transform a flat sheet of metal into metal parts that are durable and lightweight. Bending, shearing, punching, and hydroforming are all examples of processes that are used to form or cut metal sheets into the desired shape. The tools for these processes will be set up …
Recommended Practices for Stud Welding
1. Process Description. Stud welding is a general term for joining a metal stud or similar part to a workpiece.1 Welding can be done by a number of welding processes including arc, resistance, friction, and percussion. The arc stud welding process (SW), including capacitor discharge methods, will be covered in this document.
Stick Welding Sheet Metal? Here is How!
Stick welding sheet metal can be done by welding DC electrode negative with 20-40A which is about the the lowest amperage settings that still allows to strike an arc. Suitable electrodes are E6011 for …
What Are The Development Advantages Of Energy Storage Spot Welding …
Driven by industrial development, the development of the welding machine industry is also very rapid. The types and number of products are constantly increasing. Energy storage welding machines are one of them. 1. Large current. The instantaneous current of the ...
Welding Cost Estimation, Calculation and Cost Reducing Methods
Welding Cost Estimation Steps. After determining many factors that affect welding cost, now we think of how to estimate welding cost using various steps and formulae. 1. Electrode Weight – To determine the weight of the electrode, the following equation is used. E = W/Dp.
All You Need to Know About Sheet Metal Welding
Choose a Small Wire Diameter. When welding sheet metal using the MIG welding process, you should always choose a small wire diameter. A small wire diameter requires less heat to melt. It also produces a smaller weld …
How Metal Fabrication Helps Energy Storage Systems
Metal fabrication techniques are used to create tanks that are precisely manufactured to meet the specifications of the energy storage system. The tanks are designed to be …
Home
In this paper the laser micro welding process of copper material and 18650 cells is analyzed to describe the influence of process parameters (laser power, …
A Comprehensive Guide to Welding Thin Metal
MIG welding is the most common technique welders use for thin metals. Here are the steps you need to take for this process. 1. Choose the Right Shielding Gas. MIG welding works in tandem with the shielding gas, which prevents the weld from oxidizing. The shielding gas also affects the weld bead''s appearance.
Spot Welding Means, Principle, Equipment, Applications and Jobs
Some key resistance welding applications include-. 1. Automotive Industry (car body assembly) – Spot resistance welding is the main method for joining sheet metal components in the automotive industry, especially in the assembly of car bodies. It is used to create strong bonds between panels and structural components.
China Sheet Metal Fabrication|China Sheet Metal Manufacturer-ACE Sheet Metal_Leading Sheet Metal …
Established in 2002, ACE Sheet Metal has consistently upheld its dedication to delivering top-tier precision sheet metal parts and welded construction manufacturing, integrated assembly and testing services. Over the years, we have evolved into one of China''s top ...
Resistance Welding Guide
There are at least seven important resistance-welding processes. These are: Flash welding. High frequency. Percussion welding. Projection welding. Resistance seam welding. Resistance spot welding (most common process), involves the use of water-cooled copper electrodes which are clamped with the sheets into place.
Sheet Metal Design Considerations: Energy Storage Enclosures
Choose the appropriate welding method: Welding is the next step after bending a single metal sheet. Cabinets or enclosures assembled by welding are …
Sheet metal fabrication: the manufacturing & design guide (2021 …
The manufacturing & design guide. Learn how to effectively design sheet metal parts. This guide starts with the basics and moves toward design best practices and advice on material selection, finishings and fastenings, with a focus on two sheet metal fabrication processes: bending and laser cutting. Part 1.
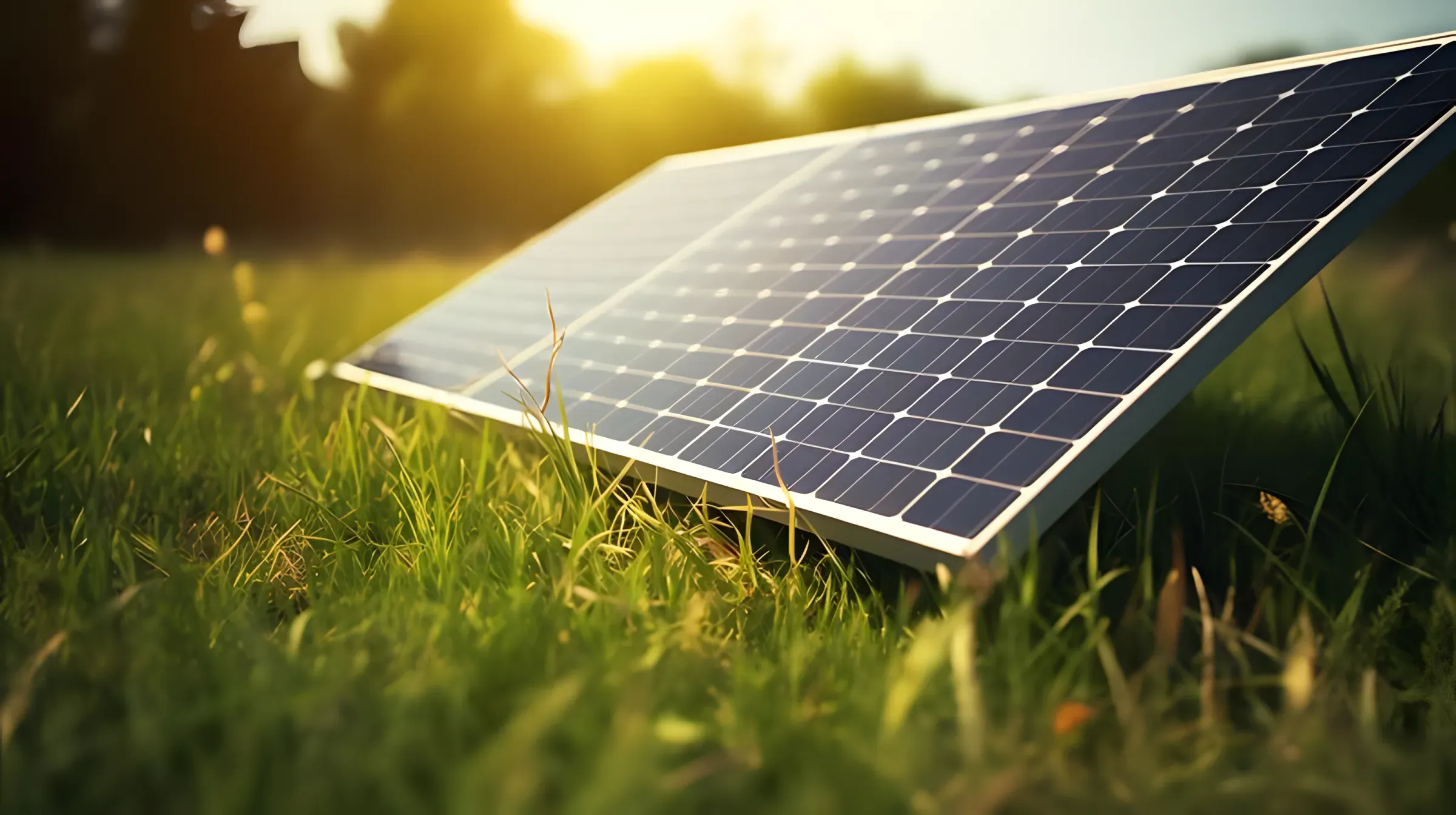
More Articles
energy storage precision sheet metal
energy storage sheet metal design
electrical energy storage cabinet sheet metal parts
energy storage cabinet sheet metal supplier
aluminum welding process with energy storage welding machine
tirana fully automatic energy storage welding machine supplier
what are the dc energy storage spot welding machines in china and europe
energy storage welding column machine price
development prospects of energy storage battery process engineers
commondoubt
Because each customer's needs are different, the price is also different. If you are interested in our products, please contact us by email and we will give you a reference price based on your needs.
You can contact us through any "Contact" option on the page and we will contact you within 24 hours.
We will have dedicated personnel to contact you. If you encounter any problems during use, you can call us and we will solve them for you as quickly as possible.
Our sales staff will recommend the most suitable products to you according to your needs and ensure that all your needs are met at the cheapest price.
Sunday: 10AM - 8PM
Fengxian District